Gleason Gear Design Manual
- Gleason gear design manuals, Dana Spicer instruction manuals, technical bulletins and General Motors repair manuals. We have personally experienced good results using the techniques in these instructions while setting up over forty thousand differentials. Ring and pinion gears are designed to be set-up and run with exact tolerances.
- 38 Gear Techno'iogy coupling, it is usually necessary that the blank design con-tai.n no projections beyond the root line of the teeth. For proper clearance, the nearest projection should be at least 1/32. below the root line. In designing a Fixed Curvic Coupling it is essential to con-sider the method of bolting or clamping the two members.
- Industrial Machinery Manuals Is Proud To Offer 1 Quality Bound Copy Of A: Gleason 1951 Spiral Bevel Gear Systems Manual This Manual Covers Models: Reference Information This Manual Includes: This System for the Design for Spiral Bevel Gears is a revision of the original Gleason System adapted by the AGMA in 1922 and revised in 1942.
Gleason publications include most of the informa- tion required by the gear designer to select a satisfactory pair of bevel gears. The pitch cone apex-to-crown value is determined by a formula that is a function of the pitch diameter, pitch angle and addendum; therefore, the pitch cone apex-to-crown-value cannot be chosen arbitrarily.
Gear Calculation
The main objective of this introductory course is to provide the basic handling and understanding of the KISSsoft® program, its user interface and the calculation possibilities. With the help of prepared exercises, participants will learn how to operate and apply the software correctly and efficiently in the design process.
Topics
Based on a helical gear pair calculation, participants will learn about:
- General settings.
- Maintenance of technology database.
- Main data input fields (basic data).
- Definition and meaning of reference profile and influence of profile shift.
- Definition of high tooth form, tolerances, tooth thickness and backlash.
- Possibilities to control the correct inputs.
- Dealing with incomplete information.
- Pre-sizing of new gears (rough sizing).
- Optimization of gear pair using different criteria such as noise, vibration or strength (fine sizing).
- Design and evaluation of profile corrections, modified tooth forms.
- Manufacturing data for drawings.
Upon Completion
A certificate is issued with successful completion.
Spur gears are a cylindrical shaped toothed component used in industrial equipment to transfer mechanical motion as well as control speed, power, and torque. These simple gears are cost-effective, durable, reliable and provide a positive, constant speed drive to facilitate daily industrial operations.
At Grob, Inc., we manufacture our own tooling, allowing us the flexibility to fabricate standard or custom cold rolled spur gears designed to meet exact specifications across a wide range of industrial applications.
What Is a Spur Gear?

Spur gears are one of the most popular types of precision cylindrical gears. These gears feature a simple design of straight, parallel teeth positioned around the circumference of a cylinder body with a central bore that fits over a shaft. In many variants, the gear is machined with a hub which thickens the gear body around the bore without changing the gear face. The central bore can also be broached as to allow the spur gear to fit onto a spline or keyed shaft.
Spur gears are used in mechanical applications to increase or decrease the speed of a device or multiply torque by transmitting motion and power from one shaft to another through a series of mated gears.
Important Spur Gear Terms and Definitions
The design and construction of a spur gear significantly influence its performance. To do their jobs effectively and efficiently, they need to be fabricated from high-quality materials and to precise dimensions. The dimensional measurements of each feature are integral to how a specific gear functions. As such, when an industry professional requires a new spur gear design or a replacement spur gear, it is imperative that they are familiar with the terms for each gear part and their respective measurements to ensure clarity and accuracy in the production or purchase order.
Some commonly used spur gear terms include:
. Pitch Circle: The circle derived from a number of teeth and a specified diametral pitch. The circle in which tooth spacing or profiles are established from which tooth proportions are constructed.
. Diametral Pitch: Ratio of the number of teeth to the pitch diameter.
. Pitch Diameter: Is the diameter of the pitch circle. This is where a spur gears angular velocity is measured. This is also a critical component for determining center distances between mating spur gears.
. Center Distance: The distance between two gears, measured from the center shaft of one gear to the center shaft of the mating gear. This can be found roughly by taking the radius of each spur gears pitch circle and adding them together.
. Module: The ratio of the reference diameter of the gear divided by the number of teeth. Module is the metric equivalent to diametral pitch.
. Addendum: The height by which a tooth projects beyond the pitch circle.
. Dedendum: The depth of a tooth space below the pitch circle. Generally greater than the addendum of the mating gear to provide clearance.
. Outside Diameter: The diameter of the addendum circle, or the circle along the outermost points of a spur gear’s teeth. This measurement is the largest diameter spur gears have.
. Root Diameter: The diameter at the base of the tooth space.
. Pressure Angle: The angle at a pitch point between the line of pressure which is normal to the tooth surface, and the plane tangent to the pitch surface.
. Whole Depth: The total depth of tooth space, equal to the addendum plus the dedendum.
Spur Gears Applications
Spur gears are used to transfer motion and power from one shaft to another in a mechanical setup. This transference can alter machinery’s operating speed, multiply torque, and allow for the fine-tuned control of positioning systems. Their design makes them suitable for lower speed operations or operational environments with a higher noise tolerance.
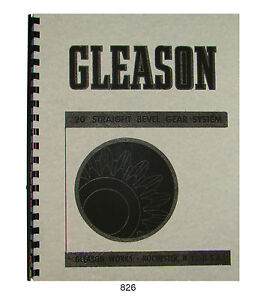
Some of the typical industrial applications include:
- Transmissions
- Conveyor systems
- Speed reducers
- Engines and mechanical transportation systems
- Gear pumps and motors
- Machining tools
Advantages
Spur gears provide several benefits to industrial applications and processes, including:
- Simplicity. Spur gears feature a simple, compact design that makes them easy to design and install, even in limited or restricted spaces.
- Constant Speed Drive. These gears increase or decrease shaft speed with a high degree of precision at a constant velocity.
- Reliability. Unlike other power and motion transmission components, spur gears are unlikely to slip during operation. Additionally, their durability decreases their risk of premature failure.
- Cost-Effectiveness. The simplicity of their design also allows for greater manufacturability, making them less expensive to fabricate and purchase even with highly specific or customized dimensions.
- Efficiency. Spur gear systems have power transmission efficiencies between 95% and 99% and can transfer large amounts of power across multiple gears with minimal power loss.
Standard and Custom Spur Gears at Grob, Inc.
At Grob, Inc., we specialize in fabricating standard and custom spur gears to suit every industrial process and application. We offer a range of dimensional capabilities (such as outer diameters up to 6 inches) and material options (including aluminum and mild to medium carbon steel) to meet our customers’ exact needs.
Gleason Total Gear Solutions
. Standard/Stock Spur Gears
Our facility is equipped to produce standard spur gears with the following characteristics:
- Cold rolled aluminum or carbon steel construction materials with high-quality surface finishes
- AGMA 6-8 quality
- 5° or 20° pressure angles
- Diametral pitches of 6–48 teeth per inch
- Modules of 0.6–4 millimeter per teeth
- Outside diameters of up to 6 inches
.Custom Spur Gears
If you need a custom spur gear, our facility can deliver you a customized solution tailored to your unique specifications. Our custom spur gear capabilities allow for modifications to the following design elements:
- Major diameter, or outside diameter
- Minor diameter, or inside diameter
- Backlash, which allows for lubrication and thermal expansion without significantly altering the functionality of the machinery
Spur Gear Production – Our Cold Rolling Process:
To produce our spur gear stock, we employ a custom cold roll forming process—called Grob Rolling. This process allows for stronger gear teeth with superior surface.
Spur Gears That Meet Your Specifications
Gleason Gear Cutter
If your facility needs high performance, durable spur gears, Grob, Inc. is here to help. Our expert team of engineers and technicians can provide standard or produce custom spur gears based on your design files to suit the exact specifications of your application.
Gleason Gear Ratios
For more information on our standard or custom cold forming capabilities or to receive a quote, contact us today.
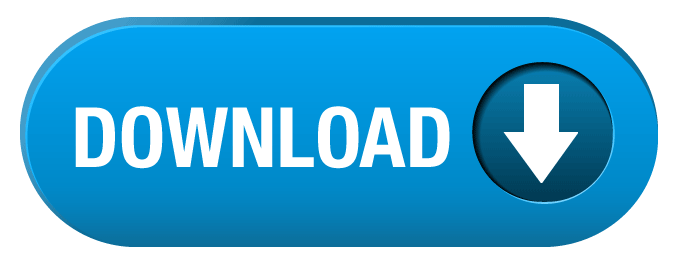